
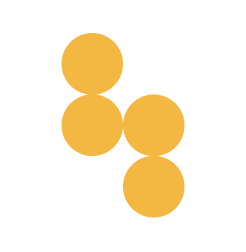
CORPORATE SOCIAL RESPONSIBILITY AND ACTIVITIES
As an embodiment of Tempo Scan’s Core Values, namely Honesty, Equality, Usefulness, Responsibility and Hard Work, which have upheld as foundational principles for over 71 years PT Tempo Scan Pacific Tbk (“Tempo Scan”) remains committed to maintaining integrity and contributing to the greater good. Tempo Scan continuously advances its Corporate Social Responsibility (“CSR”) initiatives in alignment with the Indonesian government’s vision to improve the quality of life for all stakeholders. These efforts area carried out systematically across all business activities as part of the company’s dedication to inclusive and sustainable development.
Environments
As part of its operational strategy and initiatives, Tempo Scan implements a range of programs focused on environmental protection and conservation, including the following:
1. Efficient and environmentally friendly use of energy
Energy plays a crucial role in both production process and various supporting activities within manufacturing and operational facilities. Tempo Scan relies on multiple energy sources, primarily electricity provided by state-own electricity companies (PLN) and private electricity suppliers in the industrial zones where the manufacturing facilities are located. Aditionally, Tempo Scan utilize natural gas to generate steam and diesel for backup power generation units. Currently, Tempo Scan is also exploring the adoption of renewable energy solution, including the installation solar panels in wider scale.
As part of its Key Performance Indicator (KPI), particularly within the Manufacturing division, Tempo Scan consistently monitors and manages energy consumption to support its commitment to energy efficiency and conservation. This division has made strides towards adopting more environmentally friendly energy sources, including the successful conversion of steam generators fuel from diesel to natural gas. This initiative has been fully implemented across production facilities within the Pharmaceutical Manufacturing Group (PMG) and Beverage & Nutrition Manufacturing Group (BNMG).
As the next step toward sustainable energy practices, the Manufacturing division has started the use of solar photovoltaic (Solar PV) panels for preheating boiler feed water as a pilot project. In line with the decreasing cost of solar technology, Tempo Scan is currently evaluating the broader implementation of solar panels across all manufacturing facilities. This initiative aims to integrate solar energy through a hybrid system that complements the existing electricity supply.
In addition to energy source conversion, a core strategy for energy conservation focuses on reducing energy consumption per unit of production at each manufacturing facilities. These energy-saving efforts are embedded in the factory management’s Key Performance Indicators (KPIs) and are measured and monitored on daily basis. KPI targets are established based on the principle of continuous improvement, with the expectation of year-over-year improvements.
Energy conservation efforts begin with building awareness across all levels of employee level, making it as the primary focus. From a technical standpoint, energy efficiency is also closely tied to production line performance, which is assessed using the Overall Equipment Efficiency (OEE) metric. OEE reflects the reliability, productivity and quality of equipment; a higher the OEE score indicates more efficient energy use, as more products are manufactured with lower energy input. Improving OEE is pursued through various initiatives, including preventive maintenance, equipment reconditioning, and rejuvenation using modern technology, all of which have demonstrated significant positive impacts on energy efficiency.
Moreover, when evaluating and selecting new machinery or technology, the Manufacturing division incorporates energy consumption level as one of the key considerations in decision-making process.
The second focus on energy-saving efforts is minimizing energy losses throughout production process. Steam, as a key energy element in manufacturing is carefully monitored and controlled to ensure optimal efficiency. For example, steam pressure, which represent its energy level, is maintained in accordance with production requirement to avoid unnecessary losses caused by pressure drops.
Condensate loss management is another critical area. As condensate retain substantial thermal energy, it is reused through a recovery system to preheat other processes. The remaining condensate is returned to the steam generator as boiler’s feed water, significantly reducing the energy required to heat the feed water from ambient temperature. Additionally, flue gas emitted from the steam generator chimney, which still contains high heat energy, is utilized to pre-heat boiler feed water via an economiser unit, a heat recovery system currently implemented at the BNMG Milk Powder factory. Furthermore, the use of modular steam generators system in several facilities has further contributed to more efficient energy utilization.
A third major area of focus is the compressed air system, a substantial consumer of electricity. Energy efficiency is improved through regular maintenance, leak prevention and pressure optimization to reduce compressor workload.
Next, in the area of Heating, Ventilation & Air Conditioning (HVAC), which represent one of the largest energy consumption segments in manufacturing, Tempo Scan has implemented several measures. These include replacing air-cooled chiller with more energy-efficient water-cooled chiller, utilizing thermal storage tanks to enhance HVAC performance and optimizing and air pressure balance between rooms via Building Automation System (BAS). The BAS automatically regulates temperature and humidity within the production facilities, further enhancing energy efficiency.
Finally, Tempo Scan has initiated the gradual replacement of conventional electric motors with highefficiency motors equipped with frequency converters to reduce electricity consumption. Similarly, the phase replacement of traditional tube lamps (TL) with energy-efficient LED lighting is also underway.
2. Water Conservation
At the core of Tempo Scan’s water conservation program is effective water management, guided by the 3R principle: Reduce, Reuse and Recycle.
The first principle (first R) – Reduce- focusing on minimizing water consumption through multiple initiatives. These include regular maintenance of water pipelines to prevent leaks and the optimization of production equipment cleaning processes via both Cleaning-In-Place (CIP) and offline cleaning methods, without compromising cleaning effectiveness. Adjustments are made systematically by modifying the CIP computer programs, establishing, and testing enhanced cleaning standard operating procedures (SOP) and conducting validation protocol before implementing new cleaning procedures. In addition, behavioural change among employee is promoted through ongoing training and regular water saving campaigns.
The second principle (second R) – Reuse – is implemented by utilizing water from final rinsing stages in CIP for initial rinsing cycles. This internal reallocation helps reduce overall water consumption without affecting process hygiene.
The third principle (third R) – Recycling – involves the treatment of wastewater from production process and domestic use. Wastewater is process at on-site wastewater treatment plant (IPAL) through multiple stages, including separation process, aerobic and anaerobic treatments to reduce Biological Oxygen Demand (BOD) and Chemical Oxygen Demand (COD) in compliance with regulatory standards. All manufacturing sites area equipped with IPAL facilities and treated water is further process for reuse, such as for gardening purposes. In addition, infiltration wells for rainwater have been installed across factory location to support groundwater recharge.
Water usage is also incorporate into each factory’s operational KPIs, with increasingly stringent target set annually. This approach drives continuous improvement and reinforce Tempo Scan’s commitment to sustainable water conservation.
3. Air Emission Management
Air emissions at all manufacturing facilities are routinely monitored to ensure compliance with applicable regulatory standards. The results are regularly reported to the relevant authorities as part of the company’s commitment to environmental accountability.
Tempo Scan has also initiated to replace ozone depleting refrigerants used in factory cooling system with alternatives that have zero Ozone Depletion Potential (ODP), thereby reducing the company’s impact to the ozone layer.
Another key initiative to minimize air emissions involves transitioning the energy source for steamgenerating units from diesel fuel to natural gas. This switch significantly improves the quality of air emissions and aligns with the company’s broader sustainability goals.
4. Waste Management
Waste generated from Tempo Scan’s manufacturing activities is also managed in according with the 3R principles: Reduce, Reuse and Recycle.
The first R – Reduce - is implemented through ongoing efforts at each factory site to enhance production processes and efficiency, thereby minimizing the generation of material. One notable initiative includes gradual reduction of plastic packaging in production by replacing with reusable stainless steel containers.
The second R – Reuse - involve the reuse of packaging materials, such paperboard boxes used to transport packaging materials from the packaging factory to the production sites. These boxes are returned reuse under strict quality control measures.
The third R – Recycle - is carried out in partnership with certified vendors. Packaging materials that can no liner be used in production, such as paperboard boxes, plastic drums, paper drums are evaluated for the residual commercial value and sold to authorized reprocessing companies for recycling. In addition, the company has made significant strides in selecting recycleable packaging materials, such as using PET plastic bottle that are fully recycleable.
For hazardous waste (B3), Tempo Scan ensure strict compliance with environment regulations. This type of waste is stored in a licensed temporary storage facility before being transported and processed certified hazardous waste management companies, in accordance with the applicable environmental authority guidelines.
5. Mechanism for complaints about environmental problems
Tempo Scan has established a formal mechanism for managing complaints related to environmental issues, as outlined in the Standard Operating Procedures (SOP) for Internal and External Keselamatan dan Kesehatan Kerja (K3). The procedures define external communication on Occupational Safety and Health (K3) and Environmental Protection as any of information between Tempo Scan and external parties concerning the K3 Management System, including environmental matters. Safety Health & Environment (SHE) Committee has been established and actively operates at each manufacturing sites. One of the committee’ key responsibilities is to maintain consistent engagement with relevant regulatory authorities, supporting efforts to enhance the company’s overall environmental management performance.
6. Certification/Permit in the environmental sector:
Tempo Scan ensures full compliance with environmental management certification and permitting requirements as mandated by applicable regulations. Each manufacturing facility consistently reports its environmental management efforts through the submission of Environmental Management and Monitoring Efforts (UKL-UPL) document to the relevant government authorities on regular basis.
Employment Practices, Occupational Health, and Safety
1. Equality in employment opportunities
Tempo Scan operates across nearly all region Indonesia through its Distribution and Sales Operations, as well as Manufacturing Facilities. In line with the company’s core values of Equality, Tempo Scan upholds an open and inclusive recruitment process, providing equal opportunities for individuals to participate as prospective employees.
The recruitment process is conducted based on the principles of meritocracy, prioritizing competency evaluation results and alignment with job qualifications, regardless of gender, ethnicity, religion, social status, or physical condition. Tempo Scan firmly believes that all individuals are created equal and should be given the same opportunities to access employment without any discrimination. This commitment to equality extends beyond recruitment, encompassing individual development and equal access to career advancement opportunities throughout the organization.
2. Work Facilities and Safety
Tempo Scan is firmly committed to providing a safe working environment for the employees. The company ensure that Occupational Health and Safety (OHS) facilities are in place to support operational activities in accordance with applicable laws and regulations. A systematic and structured Occupational Health and Safety Management System (SMK3) has been implemented across all manufacturing facilities.
This work safety procedures are embedded in the Company’s Operational Standards to ensure proper work dan compliance practices. All factories within Tempo Scan have been awarded the SMK3 certification by the Ministry of Manpower, achieving the prestigious Gold Category.
Continuous improvements efforts are conducted through structured hazard identification and risk assessment processes, supported by routine field inspection. Risk mitigation and accident prevention programs are implemented throughout investments in safety-related infrastructure and equipment.
To promote strong safety culture, Tempo Scan regularly conduct employee education and awareness campaigns. Maintenance program are rigorously followed to ensure the factory equipment and infrastructure are in safe working condition and do not pose operational risks.
In addition to the internal efforts, the company reinforces strict safety protocols for external partner, including engineering and service contractors working on-site. Regular emergency response drills are also conducted, involving all personnel within each operational unit, to enhance preparedness and response capability in the event of an incident.
3. Work Accident Rate
Tempo Scan is guided by a clear vision of achieving zero workplace accident across all business operations. To realize this vision, Occupational Safety and Health (K3) is embedded as a critical component within factory work procedures, governing both employee behaviour and safety of infrastructure. A strong safety culture is cultivated by encouraging individuals to prioritize their own safety while also promoting care and vigilance for the safety of others.
In the event of any workplace accident, a thorough root cause analysis is conducted to determine necessary preventive and corrective measures. The finding from each incident are shared with relevant personnel as part of continuous learning process, aimed at preventing recurrence.
Each factory regularly submits reports on workplace accidents statistics and the implementation of the safety management system to the relevant Manpower office, in accordance with regulatory requirements.
4. Occupational Health
Employee health is key priority for Tempo Scan, as it directly supports optimal productivity and overall well-being of the workplace. The company actively promotes a culture of healthy by encouraging employees to adopt healthy behaviour and lifestyles.
To support this commitment, occupational health clinics staffed by certified Hyperkes (Occupational Health) doctors are available at factory sites. Annual Medical Check Up are conducted to ensure employee maintain good health and continues to meet the physical requirement of their roles, particularly in relation to the specific product categories being manufactured.
In addition, Healthy Talk sessions are held regularly, covering a wide range of health-related topics to educate and engage employees.
Health information is also disseminated through internal K3 (Occupational Safety and Health) bulletins, further enhancing awareness and encouraging proactive personal health management.
Social and Community Development
1. Use of Local Manpower
Tempo Scan does not have specific policies regarding the recruitment of local manpower. However, Tempo Scan consistently prioritize the recruitment of employees from the local communities, provided they meet the necessary qualification and specifications for the available positions.
2. Local Community Empowerment
As a part of its commitment to the local communities, Tempo Scan actively empowers local resources by employing local manpower for various within the factory areas.
Additionally, the company collaborate with local cooperatives and communities for management of non-hazardous waste (non-B3).Tempo Scan supports Small-Medium Enterprise (SME) by engaging them as suppliers of goods and services, all while adhering to the principles of good corporate governance.
Concern for People in need
Tempo Scan demonstrates its commitment to the community through various initiatives, with a total value of Rp 17,6 billion. This reflects the company’s Core Values of “Responsibility” & “Usefulness” to the Nation and the Republic of Indonesia. These efforts are manifested in a range of impactful activities, including the following:
1. Pasukan bodrex Merah Putih Beraksi
For the past 18 years, since 2006, bodrex has consistently implemented Corporate Social Responsibility (CSR) initiatives. In 2024, bodrex launched a CSR program that offered free health check-ups across 8 cities in Java. This initiative aimed to provide essential health screenings to underserved communities with limited access to proper healthcare. The program successfully reached 6,000 individuals, providing free health check-ups and health consultations.
2. NEO Pejuang Rejeki
NEO rheumacyl, one of Tempo Scan’s flagship brands, is dedicated to inspiring and supporting the public in their livelihood efforts. In 2024, through its flagship program, “NEO Pejuang Rejeki”, the brand continued its CSR initiative, “NEO Pejuang Rejeki Peduli UMKM”, by providing much-needed business capital assistance to Small Medium Enterprises (SME).
The highlight of the event was the fund distribution ceremony held in Jakarta, which featured NEO rheumacyl’s Brand Ambassador, Andre Taulany.
3. Tempo Scan 100% Indonesia “Bring Back the Smiles of Palestinian Babies and Children”
Tempo Scan through the CSR program “Tempo Scan 100% Indonesia” launched the initiatives titled “Return the Smiles of Palestinian Babies and Children”. During August to September 2024, Tempo Scan raised donations of Rp 100 per product for every purchase of its products, ultimately raising a total donation of Rp 10 billion. The donations were handed over to BAZNAS RI to ensure that the aid reached Palestinian babies and children. The donation ceremony took place during the Bazar Istiqlal Tempo Scan event in November 2024.
Responsibility for Goods and/or Services
Tempo Scan has always adhered to its Core Values of Responsibility and Usefulness in creating and developing products that meet consumer needs and are safe for use. The production and marketing of high-quality products by Tempo Scan are in full compliance with standards set by National Agency of Drug & Food Control or Badan Pengawas Obat dan Makanan (BPOM), the Ministry of Health or other regulatory agencies.
The production processes and facilities follows the standards of Good Manufacturing Practices (GMP) including Cara Pembuatan Obat yang Baik (CPOB), Cara Pembuatan Obat Tradisional (CPOTB), Cara Pembuatan Kosmetik yang Baik (CPKB), Cara Pembuatan Alat Kesehatan yang Baik (CPAKB), Cara Produksi Pangan yang Baik (CPPB), Cara pembuatan Produk Perbekalan Kesehatan Rumah Tangga yang Baik (CPKRTB), and Cara Distribusi Obat yang Baik (CDOB). These standards which are continuously updated to align with the latest GMP guidelines.
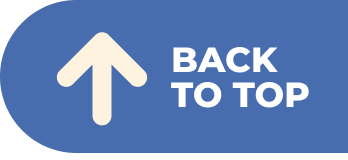